The Comprehensive Guide to Plastic Injection Moulding
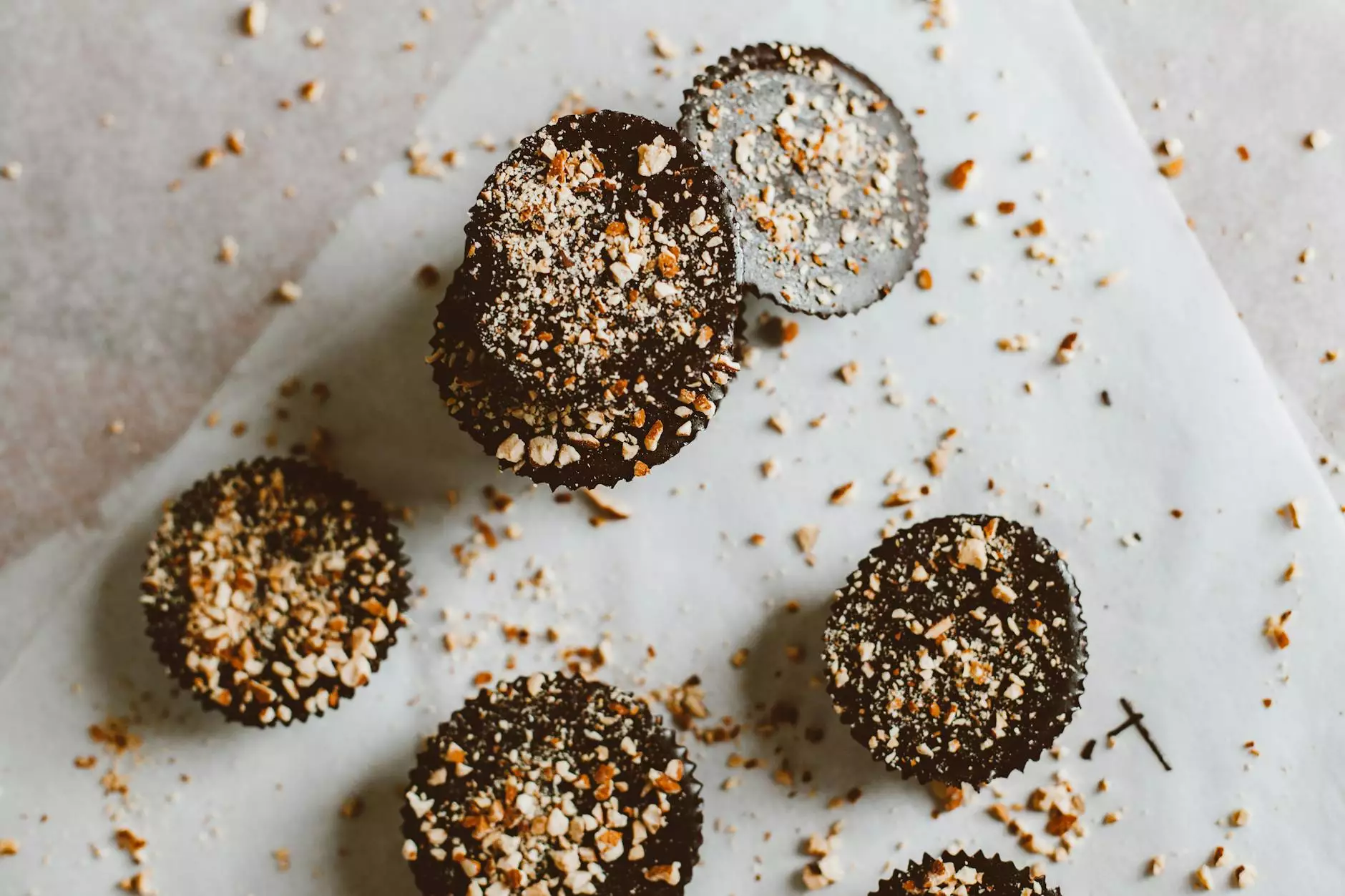
Plastic injection moulding is a revolutionary manufacturing process that has transformed the way products are designed and produced. With its ability to produce complex shapes, high precision, and scalability, it is a crucial technology in today's manufacturing landscape. In this guide, we will delve deep into the intricacies of this process, its applications, benefits, and its importance in the realm of metal fabricators. By the end of this article, you will have a thorough understanding of plastic injection moulding and its significance in the business world.
Understanding Plastic Injection Moulding
At its core, plastic injection moulding is a manufacturing process used to create items from thermoplastic materials. This pioneering process involves injecting molten plastic into a pre-designed mold, where it cools and hardens into the final product. The technology's capacity to produce large volumes of parts with intricate shapes makes it an invaluable asset for various industries.
The Process of Plastic Injection Moulding
The plastic injection moulding process can be broken down into several key stages:
- Mold Design: The first step involves creating a mold that reflects the desired shape and dimensions of the product. Engineers use Computer-Aided Design (CAD) software to fine-tune the mold design.
- Material Selection: Choosing the right plastic material is crucial for achieving the desired physical properties of the final product. Common materials include ABS, polypropylene, and polystyrene.
- Melting the Plastic: The selected plastic is fed into the injection molding machine, where it is heated until it reaches a molten state.
- Injection: The molten plastic is then injected into the mold under high pressure, filling every cavity to ensure accurate detailing.
- Cooling: Once filled, the mold is kept cool, allowing the plastic to harden and take the shape of the mold.
- Ejection: After cooling, the mold opens and the finished part is ejected.
Applications of Plastic Injection Moulding
The versatility of plastic injection moulding lends itself to a wide array of applications across multiple industries. Here are some of the most prominent ones:
1. Consumer Products
Familiar items that we use daily, such as containers, toys, and household goods, are often manufactured using plastic injection moulding. This process allows for mass production at a low cost, making it ideal for consumer goods.
2. Automotive Industry
In the automotive sector, plastic injection moulding is crucial for producing components such as dashboards, panels, and trim pieces. Its precision ensures that parts fit together perfectly, enhancing vehicle safety and aesthetics.
3. Medical Devices
The healthcare sector relies heavily on this technology for manufacturing medical devices and equipment. Products like syringes, surgical instruments, and housing for electronic devices must meet strict regulatory standards, making precision critical.
4. Electronics
In electronics, plastic injection moulding is utilized for creating housings and components for devices like smartphones, laptops, and more. The process permits intricate designs that are both beautiful and functional.
Benefits of Plastic Injection Moulding
Utilizing plastic injection moulding offers numerous advantages that can significantly impact a business’s efficiency and product quality:
1. Efficient Production
This method allows for high-volume production with consistent quality. Once the mold is built, each cycle can produce parts quickly, leading to reduced manufacturing time and higher output.
2. Design Flexibility
The ability to create complex shapes and intricate designs makes plastic injection moulding an excellent choice for innovative product development. It supports both high-and low-volume projects.
3. Cost-Efficiency
While the initial investment in molds can be quite high, the long-term savings achieved through mass production often outweigh these costs. Furthermore, the ability to use recycled materials is a significant economic plus.
4. Reduced Waste
The precision of plastic injection moulding means that less material is wasted during production compared to other manufacturing methods. The process is capable of producing parts with minimal scrap, enhancing sustainable practices.
The Role of Metal Fabricators in Plastic Injection Moulding
Although plastic injection moulding focuses on plastic products, the role of metal fabricators is integral in this manufacturing process. Here’s how:
1. Creating Molds
Metal fabricators are often responsible for designing and manufacturing the molds used in plastic injection moulding. These molds must endure high pressure and temperature, requiring expert knowledge in metallurgy and fabrication techniques.
2. Maintenance of Equipment
Metal fabricators also play a crucial role in maintaining and repairing the machinery used in the injection molding process, ensuring everything runs smoothly and efficiently.
3. Collaboration in Design
Collaboration between plastic injection engineers and metal fabricators is essential. Discussing material selections, mold designs, and production processes can lead to better product outcomes and innovations.
Challenges in the Plastic Injection Moulding Process
Despite its numerous advantages, plastic injection moulding does come with its own set of challenges:
1. High Initial Costs
The upfront investment in molds and machinery can be significant. Small businesses may find it challenging to fund these initial costs while still ensuring a profitable operation.
2. Material Limitations
Not all plastics are suitable for injection moulding. The selection of material can affect the properties and functionality of the final product, limiting designers in their choices.
3. Complexity of the Process
While plastic injection moulding allows for complex designs, those complexities can introduce challenges in production, such as longer cycle times and the need for precise control over conditions.
Future Trends in Plastic Injection Moulding
The landscape of plastic injection moulding is evolving. Here are some key trends to watch:
1. Sustainable Practices
As environmental concerns grow, the demand for sustainable materials and methods increases. Companies are exploring biodegradable plastics and recycling initiatives to enhance their eco-friendliness.
2. Advanced Technologies
New technologies, such as 3D printing and smarter, automated injection molding systems, are emerging. These innovations can streamline processes and reduce production costs.
3. Customization
With the rise of personalization in products, plastic injection moulding will see an increase in demand for custom molds and short-run production capabilities, allowing businesses to cater to niche markets.
Conclusion
In summary, plastic injection moulding is a vital process in modern manufacturing that ensures efficiency, precision, and versatility. Its applications range across industries, making it indispensable for metal fabricators and manufacturers alike. As trends towards sustainability and advanced technology continue to shape the industry, understanding the complexities and advantages of this method will be crucial for businesses looking to thrive in a competitive market. Embracing plastic injection moulding not only meets the demands of today but prepares companies for the innovations of tomorrow.
For more information about plastic injection moulding and how it can benefit your business, visit deepmould.net.