Understanding the Benefits of Silicone Membrane for Vacuum Press Applications
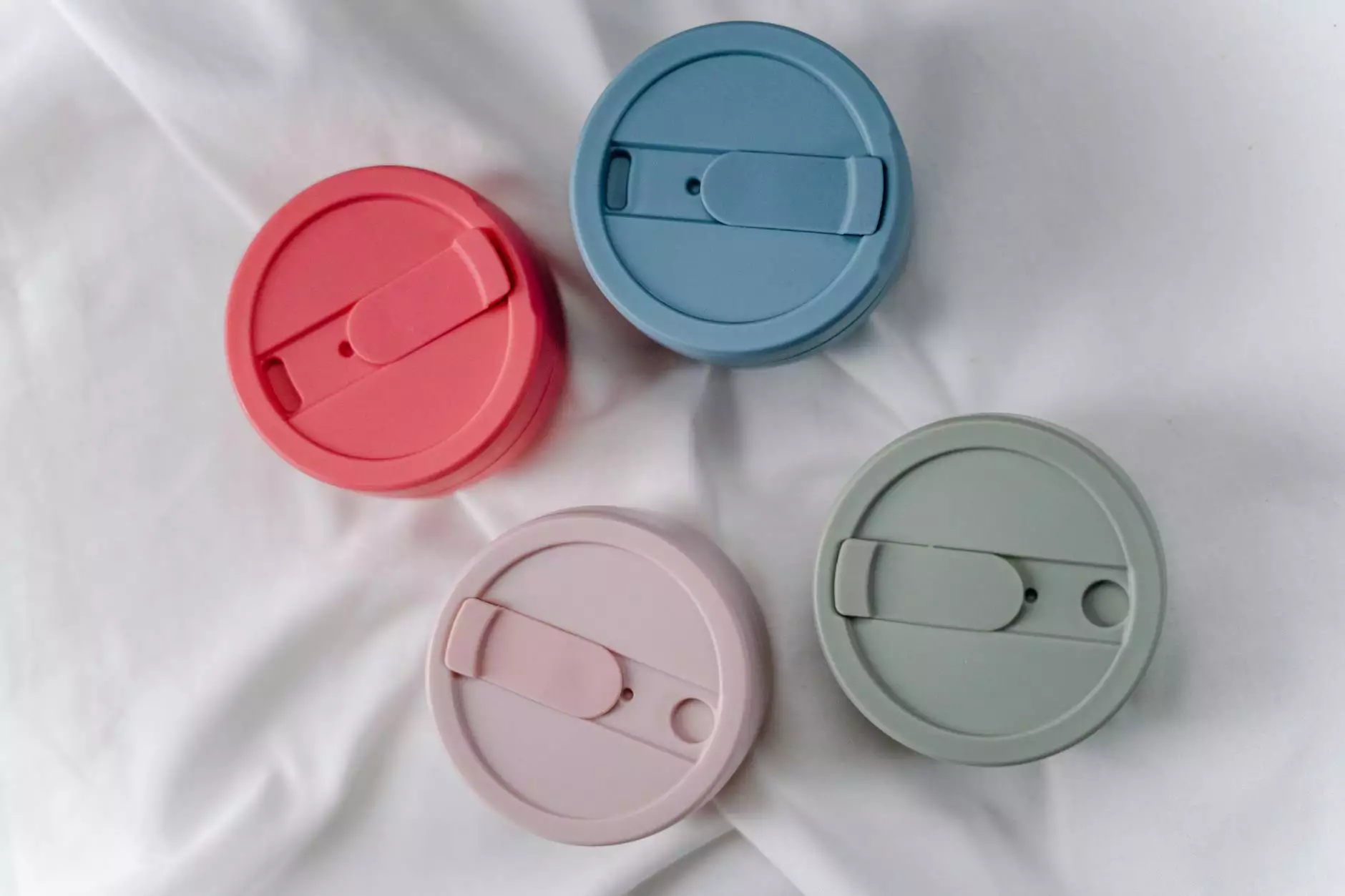
Silicone membranes for vacuum press applications offer an unmatched level of versatility, efficiency, and durability, making them a preferred choice across various industries, including health & medical, beauty & spas, and medical spas. As industries evolve and demand higher quality materials, the role of silicone membranes continues to grow, unlocking new possibilities for precision and innovation.
What is a Silicone Membrane?
A silicone membrane is a flexible, durable material made from silicone polymers. These membranes are designed for use in vacuum press systems, which apply even pressure during processes such as laminating, pressing, and sealing. The inherent properties of silicone, including its high elasticity, temperature resistance, chemical stability, and biocompatibility, make it ideal for various applications.
The Importance of Vacuum Press in Industries
Vacuum pressing is a technique widely used in multiple sectors, playing a crucial role in obtaining high-quality products. By removing air from the press before applying heat and pressure, manufacturers can achieve a better bond and a smoother finish. Industries that benefit from vacuum pressing include:
- Furniture Manufacturing: For laminating veneers and surfaces for enhanced aesthetics.
- Medical Industry: Producing sterile components and devices.
- Automotive Industry: For creating lightweight composite materials.
- Construction: Making strong, resilient materials for building applications.
Benefits of Using Silicone Membranes in Vacuum Press Applications
1. Enhanced Durability and Longevity
One of the standout features of silicone membranes for vacuum press technology is their exceptional durability. Unlike traditional materials, silicone membranes are resistant to wear and degradation over time. This means that they can withstand repeated use in harsh working conditions without losing their effectiveness.
2. Heat Resistance
Silicone can endure a wide range of temperatures, making it suitable for various vacuum press processes that require heat application. This heat resistance ensures consistent performance, maintains the integrity of the materials being pressed, and avoids potential failures that could arise from material deformation.
3. Chemical Stability
Silicone membranes demonstrate excellent chemical stability, allowing them to resist degradation from various chemicals commonly used in industrial applications. This property makes them invaluable in environments where exposure to solvents, oils, or acids is inevitable.
4. Flexibility and Conformability
The intrinsic flexibility of silicone membranes allows them to conform to complex shapes and surfaces. This ability results in enhanced surface contact during pressing, leading to superior adhesion and an even finish. The ability to adapt ensures that a silicone membrane can be used effectively across different projects.
5. Biocompatibility
Particularly in the health and medical sectors, the biocompatibility of silicone is of utmost importance. Silicone membranes are safe to use with medical-related products, ensuring that they do not induce adverse reactions when in contact with skin or bodily fluids. This characteristic makes them essential for applications in medical spas and health services.
Applications of Silicone Membranes in Different Industries
1. Healthcare and Medical Industry
In the medical field, the pressure application provided by silicone membranes during vacuum pressing is crucial for producing sterile components and packaging. Their reliability aids in maintaining the required sterility, which is essential in surgical settings.
2. Beauty and Spa Industry
In the beauty industry, silicone membranes are used extensively for developing products such as facial masks and spa treatments. The effectiveness of vacuum pressing with silicone ensures that active ingredients are evenly distributed and effectively absorbed into the skin.
3. Medical Spas and Aesthetic Treatments
Medical spas use silicone membranes in various therapeutic treatments. The precision and reliability of vacuum pressing help improve the quality of aesthetic devices, ensuring that they meet the high standards required for patient safety and satisfaction.
Choosing the Right Silicone Membrane for Your Needs
Selecting the appropriate silicone membrane for vacuum press requires understanding specific project requirements. Here are some vital factors to consider:
- Thickness: Thicker membranes provide durability, while thinner ones offer flexibility.
- Temperature Rating: Ensure the membrane can withstand the temperatures used in your specific press process.
- Size: Choose the size that best fits your vacuum press equipment for optimal performance.
- Surface Texture: The texture can affect how well materials adhere during the pressing process.
Maintenance and Care of Silicone Membranes
Proper maintenance of your silicone membranes will ensure their longevity and reliability. Here are some tips:
- Regular Cleaning: Use mild detergents and avoid harsh chemicals that could degrade the silicone.
- Inspection: Regularly check for tears, punctures, or signs of wear that could impact performance.
- Proper Storage: Store membranes flat or rolled to prevent creasing or damage.
Conclusion
In conclusion, the versatility and reliability of silicone membranes for vacuum press applications make them an essential component in various industries, including health and medical, beauty, and medical spas. Their unique properties—such as durability, heat resistance, and biocompatibility—ensure that they meet the high standards required in today’s fast-paced market. By selecting the right silicone membrane for your needs and maintaining it properly, you can leverage its many benefits and enhance your production processes.
For high-quality silicone membranes that meet your pressing needs, visit silicone-membranes.eu. Experience the difference that premium silicone products can make in your operations today.